製造業によくあるポカミス…できるだけミスをしないための対策・防ぎ方
製造業に勤めている人の中で、できる限りミスをしないための対策や方法を知りたいと考えている人に、今回の記事はおすすめです。ポカミスは人的ミスが原因で発生するといわれています。同じようなミスを繰り返していると、顧客に迷惑がかかってしまい、顧客が製品を購入しなくなることも考えられます。きちんと対策を講じましょう。
製造の現場でよく聞く「ポカミス」とは
人間は必ずミスしますが、そのミスが原因で不良品が発生することも考えられます。顧客満足度が低下してしまうので、極力発生しないように気を付けなければいけません。
ポカミスとは
人的ミスのことを指します。うっかりミスともよばれていますが、思いがけずミスしてしまうことで、不良品の発生率が高くなってしまうことがあります。そして、不良品が発生することで、製品を受け取った企業や顧客からクレームが来る可能性があります。また、クレームが来なくても、顧客離れにつながってしまう恐れがあるので、ポカミスはできる限り防ぐようにすることが求められています。
重要な要素
人間は機械とは異なりミスする生き物です。それはどんなに優秀な人でもミスしてしまうので、ミスを1回もしないようにしましょうと目標を掲げるのは現実的ではありません。しかし、ミスが発生した原因を知ることと、ミスをいかにして抑えるようにするかを明らかにしなければいけません。なぜなら同じようなことを繰り返してしまうからです。具体的な対策を講じることなく、同じようなことを繰り返すのは防がなくてはいけません。それが重要な要素といえるでしょう。
ポカミスが起きる原因は?
いくつかの原因が考えられるので、1つずつ見ていきましょう。人的ミスだけとは限りません。また、複合的な要因も充分に考えられます。
記憶エラー
こちらのエラーは、マニュアルや作業を覚えられない、作業を正しく継続できない、作業手順を思い出せないことが原因です。配属されたばかりの作業員であれば、熟練の作業員がサポートするかたちをとるなどして、ミスをあらかじめ防ぐことが大切です。
認知エラー
こちらのエラーは、認識を誤ったことにより生じています。見間違いや聞き間違いなどは日常生活でも頻繁に発生しますが、製造業では致命傷になります。マニュアルを活用するなどして、明確に示すことが必要です。
判断エラー
こちらのエラーは、現在の状況を正しく判断できていないことにより生じています。次の行動を間違えてしまうので、さらに状況が悪化することが予想されます。
行動エラー
こちらのエラーは、方法や手順を間違えることにより生じています。工程ごとに作業員が配置されている場合、自分の持ち場の仕事をきちんと行わなければ不良品が次々と発生してしまいます。
あえて型
こちらのエラーは、分かっているのにあえて手を抜く、横着することにより生じています。職務の怠慢が発生してしまう原因を追究しなければいけません。
製造設備に原因がある場合
複雑な機械操作によりミスが発生してしまうことや、2種類の機械を操作するときに、ボタンの判別がつかずに間違えて押してしまうことなどが考えられます。
作業環境に原因がある場合
現場の明るさに問題がある場合や、現場の温度や湿度が快適ではなかったために、注意力が欠けてしまうことなどが考えられます。
ポカミスを防ぐ3つのステップと対策方法
具体的な方法を見ていきましょう。同じようなミスを繰り返さないようにすることが大切です。
原因を解明する
ポカミスは誰でも起きてしまうので仕方ないと結論を出すのではなく、なぜポカミスが発生したのか原因を解明する必要があります。ポカミスが起きた原因が、人的ミスだけではなく、機械や設備にも原因があるかもしれません。たとえば、2種類の機械を操作するときに、ボタンの判別がつきにくいのであれば、判別がつきやすいようにボタンの色を変化させることが有効な対策案として浮上します。このように、原因を解明できると対策を講じやすくなるので、そのままにしてはいけません。
作業手順や方法の明確化
自分に与えられた持ち場をきちんと守ることが作業員に求められています。しかし、勤務環境に慣れてくると自分の勝手な解釈で作業する人も出てくるでしょう。全員が同じマニュアルで作業を進めるように統制することが求められています。
ルールや作業方法の周知と徹底
たとえば、新たな設備を導入したときには、全員に周知と徹底をしなければいけません。一部の人だけ知っている状況は避けましょう。周知と徹底をするための方法として、朝礼の場面を活用するとよいでしょう。また、定期的に行われる研修があれば、その場を活用するとよいでしょう。
まとめ
ポカミスが発生した直後から原因を明確にするために行動を起こしましょう。ミスを隠すようなことはしてはいけません。また、原因を明確にするのに時間がかかってしまうと、同じようなミスが発生する可能性があります。そして、同じようなミスを二度と繰り返さないように、すべての作業員に情報を共有します。機械や設備に問題がある場合は、新しい機械を導入するなどして勤務環境の改善にも努めましょう。
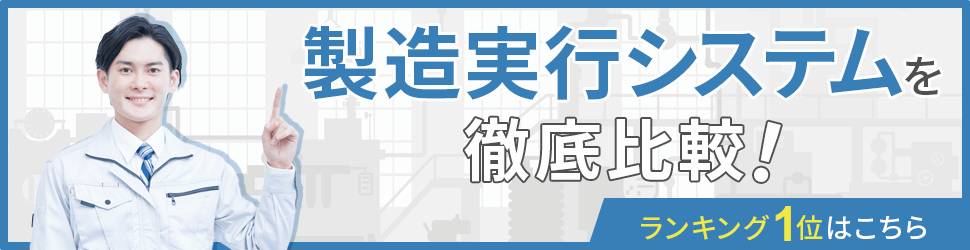
-
引用元:https://uni-face.co.jp/factoryib/ibmes/
スモールスタートで始めやすく最短1ヶ月のスピード導入可能!時間をかけずに導入したいという企業にもぴったり!-
Point
設備1台からの「トライアル導入」可能な為、スモールスタートに最適!
-
Point
エンジニアと直接ご相談可能!製造現場をよく知る開発者として具体的なプランをご提案!
-
Point
コンピュータが苦手な人でも大丈夫!直感的な操作でシステム運用の負担も軽減
-
Point