製造現場をDX化するメリットとは?実現するための課題や流れを解説!
最近のビジネス業界では、データやIT技術を活かしてビジネスに革新をもたらすDX(デジタルトランスフォーメーション)化を推進しています。それは製造業においても同じでDX化が進められていますが、はたして製造現場でDX化するメリットがあるのでしょうか。今回はDX化の実現に向けた流れや課題などを紹介します。
製造現場におけるDX化の現状
製造業は日本の全産業の中でも基幹産業のひとつで中心的役割を担っていますが、高齢化や若年層の就労人数の減少による人材不足で、労働者確保という大きな課題を抱えています。さらに、新型コロナウィルスの影響による国内外での生産活動、材料の調達、物流や配送の影響で厳しい状況におかれています。
そうした状況を解決する方法がDX化です。DXという言葉は2004年に始めて登場し、日本でも2018年に経済産業省が企業のDX化を推進してから普及し、単に作業レベルでのデジタル化だけではなく、企業文化や風土を変革することも含めて使用されています。数多くの業界で推進されていますが、DX化には導入費や保守費がかかり、導入する規模によってコストは大きく異なるため、導入をためらう企業もあり、製造業でもDX化があまり普及していません。かりに導入しても、費用の関係により全体の一部しか導入しなければ、効果が限定的になるため、企業全体として取り組むのをためらう可能性もあります。
さらに、自社の設備や工程を理解しているIT人材が必要ですが、製造業ではITの人材不足も深刻です。IT人材の育成には時間と労力がかかるため、長期的に育てていかないといけません。結果、一部の精通している人材に頼ったり、外部に委託したりするため、理解している人材が退職してしまうと社内にノウハウが蓄積されないという現象がおき、DX化が進まない状況になっているのです。
製造現場をDX化するメリット
顧客や社会のニーズが変動するのに加えて、新型コロナウィルス感染症の影響など、事前に発生や変化を予測するすることが難しい外部要因により、製造業界ではどのような商品がどれくらい売れるのかを想定するのが難しい状況となっています。そのため、製造業のDX化の重要性は高く、大きなメリットがもたらされます。
人材不足の課題を解決
製造業の大きな課題となっている人材不足を解消してくれます。今まで人が行っていた作業を機械にまかせることで製造現場の大幅な人的リソースを削減し、作業精度の安定や生産効率の向上につながります、また、採用コストや育成コストもかからないためにコスト面の削減にもなります。
生産効率の向上
IT技術や機械、ロボットなどの活用により、大幅に人を減らした現場でも生産効率を維持、向上させることが可能です。また、現場でリアルタイムに収集したデータを活用することで、最適なスケジュールや生産量などが分かります。
企業価値があがる
DX化することで、現場レベルでの向上だけでなく、ビジネスモデルに変革をもたらすことが重要です。DX化により現場で余裕が生まれてきたリソースを、新たな製品開発や品質の向上に力を入れることで、企業価値をあげることが可能です。
製造現場をDX化するまでの課題
製造現場をDX化するのは簡単ではありません。DX化を進めていくためにはいろいろな課題がありますが、とくに製造業では3つの主な課題があります。
人材不足
多くの人手を必要としてきた製造業界にとって労働人口の減少は大きな課題です。そこで、人材確保が重要となってきますが、適切な人材を確保することが困難になっています。また、現場では特定のスキルを持った人に仕事が偏っており、そうした方々が高齢化などを理由に企業を退職してしまうため、技術継承が困難な状況が生まれています。
古い価値観
企業の活動能力には、組織が自己変革する能力「ダイナミック・ケイパビリティ」と、今ある経営資源を有効活用し利益を最大化する能力「オーディナリー・ケイパビリティ」があります。
外部環境があまり変化しない時代には「オーディナリー・ケイパビリティ」が重要ですが、市場ニーズや外部環境が大きく変わるような不確実性の高い現代では「ダイナミック・ケイパビリティ」が求められています。しかし、国内企業の多くの企業は前者の取り組みによって利益を最大化することに追われ、組織の変革にまで辿りついている企業は少ないのです。
老朽化しているシステム
多くの製造業界の企業で、事業や業務の中核に直接関わる基幹系システムで、複雑化、老朽化、ブラックボックス化しています。そのため、活用するためのデータが整備されていなかったり、ほかのシステムとの連携が困難などを理由に、現状のまま進める企業が多く、新たな技術の導入がしにくくなっています。
製造現場をDX化するまでの流れ
それでは、どのようにして製造現場をDX化していくのがいいのか順番を追って説明します。
イメージ共有
最初に行うことは企業全体でゴールをイメージすることで、そのために製造現場で抱えている課題の解決方法を考えていきます。そうすれば、自社のDX化で何を実現していきたいかが見えてくるからです。ただし、部門ごとに取り組むと効率が悪くなるため、必ず経営陣が中心となって各部門と連携し社内全体でイメージを共有しながら進めましょう。
万全の準備
共有のイメージを明確にしたあとは、目的を達成するためにどのような人材が必要なのかを考え確保することです。さらに、データを収集し、分析することで、市場ニーズを把握し、高品質な製品を作り上げることはもちろん、潜在的な顧客のニーズの理解も進めていきます。
業務の効率化
業務全体を見直し、非効率な部分がないか点検します。もし、非効率な部分が合った場合は、自動化できないか検討します。
ここで大事なのは、変更する場合は、一気に全体を変更してしまわないことです。業務全体を急に変更してしまうと、いろいろな現場で混乱してしまうリスクや失敗したあとの負担も大きいため、まずは、各部門で小さな事から取り組むことが大切です。取り組んだ後は、必ず効果を検証し、成果を確認したうえで、次の業務効率化を図りましょう。
顧客を育成
顧客のニーズに合わせた新商品の開発だけではなく、ビジネスモデルの変革も継続して行いましょう。また、次にどのようなサービスが求められていくのかという変化を捉えるために、リアルデータを活用しながら価値を創造するための仕組みを作る必要があります。そのようにして顧客満足度をあげながら、次のニーズを察知し続けていきます。
まとめ
今回は製造現場をDX化するための課題やメリットについて紹介しました。製造業では人材不足をはじめ多くの問題を抱えていますが、そうした問題を解決してくれるのがDX化です。DX化によって、より効率的な結果を出すためには、自社がどのような課題を抱え、DX化することで何を解決していきたいかを考えておくことが大切です。
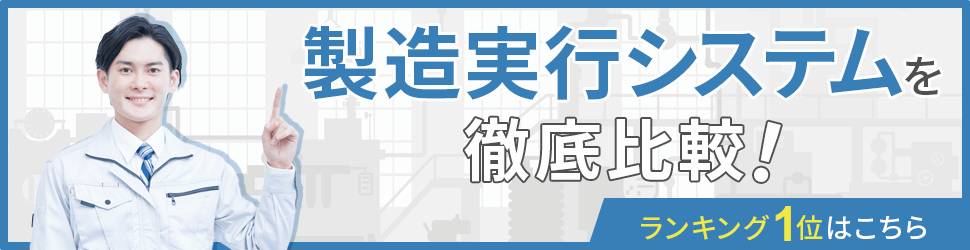
-
引用元:https://uni-face.co.jp/factoryib/ibmes/
スモールスタートで始めやすく最短1ヶ月のスピード導入可能!時間をかけずに導入したいという企業にもぴったり!-
Point
設備1台からの「トライアル導入」可能な為、スモールスタートに最適!
-
Point
エンジニアと直接ご相談可能!製造現場をよく知る開発者として具体的なプランをご提案!
-
Point
コンピュータが苦手な人でも大丈夫!直感的な操作でシステム運用の負担も軽減
-
Point